How to Use Our Products
TT4.0 Table Top Resin
TT 4.0 is a two-part epoxy resin, it is a fast curing, ultra-clear, and UV resistant coating for tabletops, counters, artwork, etc. It’s 100% waterproof, has a high scratch, stain, and yellowing resistance, and contains no VOCs. With excellent self-leveling qualities, it’s easy to achieve beautiful glossy results the first time.
User instructions
These are recommended guidelines to follow while using the TT4.0 product.
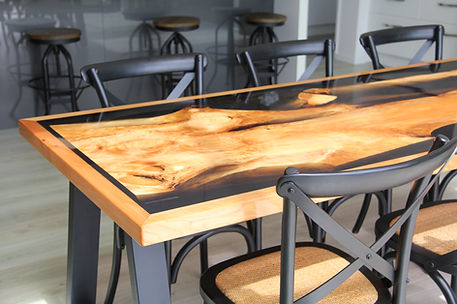
Although epoxies are becoming more user friendly with no VOC’s or solvents, it is ALWAYS best to maintain safe practices by using gloves and a respirator. Never ingest and store away from children!
Temperature is the key point when using this resin. Gel time and fully cured time are dictated by this. For best results, use in temperatures over 22deg, preferably higher for a quicker and harder set.
TT4.0 is an incredibly versatile resin. Being a medium set resin, it can be used for sealing, small void, crack and grain filling, art work and can also be flood coated to a depth of 8ml. Remember, flood coating is just that. Without enough volume of material, the self settling capabilities of the resin will be severely hindered. Use 1100grams for each sqm for final flood coating.
Through experience I have found two coats are generally necessary to get a high end result. The first coat is to seal the wood, fill the grain and any holes that might be in the wood. This coat does not need to be as thick as the final coat, and is only there to prepare and flatten the surface, ready for it’s final flood coat.
Step One: Sealing the wood
The biggest key here is something you never hear about, but is absolutey crutial to the sealing process. NEVER take a cold peice of wood into a hot room to seal. Any air inside the wood will want to escape through small vents which negates the sealing process altogether.
Certain parts of the timber will want to absorb a lot of resin. The end grain is an obvious, along with knots and rot. To achieve a good seal coat, thin the resin down 10-15% with epoxy thinners or acetone. This will make the resin more viscous, and helps the resin get absorbed into the wood. You may need to coat some areas up to 7 times with the same brew of resin until it no longer accepts sealer. Wood that has absorbed all the resin and gone dry will eventually discolour and blemish, so keep putting the resin on to avoid dry patches. After the wood no longer accepts resin, put a coat of straight (unwatered) resin on top.
Step Two: Prepare yourself.
Once the seal coat has cured, sand the table flat with 180grit sandpaper. Often there will be small voids from cracks in the wood and similar, and the quickest and easiest way to fill these is with UV resin. After sanding, clean the table and make sure everything is free of dust and surfaces have been well wiped with a rag with meths, isopropyl, acetone or prepsol. Finish with a tack rag if you have one. Make sure your table is level and the room is at a suitable temperature. Solvent free resins require the temperature to be above 20 degrees, with 25 degrees being optimum for the table top resin. It is actually very easy to control a room's temperature. We also sell temperature regulated switches that can be easily wired into a heater. We recommend you regulate ambient room temperature, rather than blow hot air over your table top. This can lead to the wood moving and wanting to twist or warp.
Step Three: Mixing the resin
Depending on the room temperature, heating the epoxy is necessary to thin down the consistency of the resin. Resin that’s too cold is like molasses. And if attempting to mix the parts, no matter how slowly you stir, you’ll trap all sorts of air bubbles. The thicker consistency also makes it hard to fully combine the two parts. For Table Top resin, you can either heat the BASE resin in the microwave at the lowest setting until warm 21-25deg (not hot.!!), or put the containers into buckets of warm water until the desired temperature is reached.. For larger mixes of resin, keep it on the cooler side of that. This warming makes the resin more viscous, and helps it’s self levelling qualities. It also reduces the amount of resin required to get a good flood coat. Use 1100grams for each sqm for final flood coating.
Always mix TT4.0 resin by weight rather than volume, as the base and hardener have different weight-volume ratios. Be EXTRA vigilant to make sure you have combined the two parts properly.!! Often changing mixing containers and re-stirring is a great way to ensure no base resin is left on the bottom of the mixing pot. Try not to create too many air bubbles whilst mixing.
Step Four: Applying the resin
Start by pouring half of your resin onto the table top. With a wide chip brush, wet out the table until you have covered the entire top and sides. This brushing is mechanically bonding the resin to the table. At this stage I give it a quick blow torch. Be aware that you don't take too much time doing this if you have a large amount of resin still sitting in the bucket. For the inexperiaced, it might be advangous to mix the two brews seperatly.Then strategically pour the remaining resin onto the table and spread it out evenly with a brush or trowel. There should be plenty of resin on the table so that it floods over the sides. Without the necessary volume of resin, the self levelling qualities will be severely hindered.
Step Five: Remove any remaining air bubbles.
Either ise blow tourch or heat gun to the air bubbles in the resin . Be very aware not to get to close, and always have the tool moving fast to avoid overheating the resin.
Step Six: Clean up
After an hour I use a stirring stick to drag along the bottom of the table, wiping the drips of excess resin away. Keep the room as dust free as possible while the resin cures, although most fine dust will sit on top of the resin and be polished out later.
DP4.0 Deep Pour Resin
DP4.0 is a specially formulated 2 part epoxy resin, specifically designed for large volume pours and making River Tables . It is slow curing (low heat), has low viscosity and excellent bubble dispersion. This resin has been designed especially for thick, crystal clear pours, and has a high-temperature resistance of up to 90 degrees (Celsius) once cured. It’s UV resistant, self-leveling, cures rock hard, and mixes well with pigments and powders.
User instructions
These are recommended guidelines to follow while using the TT4.0 product.

Although epoxies are becoming more user-friendly with no VOCs or solvents, it is ALWAYS best to maintain safe practices by using gloves and a respirator in a well-ventilated area. Never ingest and store away from children!
Temperature and the mass of the product are the key points when using deep pour resins. Gel time and fully cured time are dictated by these factors.
If pouring at very high volumes, for best results keep the room temperature between 18-21 degrees. It is recommended not to pour in less than 16deg, as the chemical reaction and crosslinking needs a certain ambient temperature to fully harden. After a period of 36-48hrs hours from pouring, the room can be warmed above 25deg to speed up the final curing process. A low and slow approach is generally the best way to tackle the larger pours. Using a fan to take any hot air away from the top of the table is essential.
For smaller and thinner pours like chopping boards etc, keep the room at a higher temperature of 23 - 26 degrees for a faster cure.
On this note, it is actually very easy to control a room's temperature. We also sell temperature-regulated switches which can be easily wired into a heater. We recommend you regulate ambient room temperature, rather than blow hot air over your tabletop. This can lead to the wood moving and wanting to twist and cup, and may overheat the resin.
Step one: Find out how much resin you will need.
There are many internet sites that help you accomplish this. Simply type in "Resin volume calculator" Being a relatively expensive product, I recommend having a second project ready to use any excess resin.
Step Two: Preparing your surface.
It is always recommended to seal the live-edge (River) and the bottom of your wood before using your deep pour resin. This is to alleviate air bubbles coming up through the resin whilst it’s setting(very important if doing clear or transparent pours!). The biggest key here is something you never hear about, but is absolutey crutial to the sealing process. NEVER take a cold peice of wood into a hot room to seal. Any air inside the wood will want to escape through small vents which negates the sealing process altogether.
Make sure your wood is dry (under 15% moisture), and remove bark and rotted areas back to clean wood. . Then apply your sealant. Certain areas of the wood will require several applications (of the same brew) until it’s finally soaked through and no longer accepting resin. After the seal coat has set, lightly sand your live edges before assembling your wood into your form/mould and clamping down. Do not clamp down excessively to allow the wood to move if slight shrinkage occurs. Never screw the wood to your mould for this reason. If the wood has twist or warping, do not try to flatten it with the clamps as it will always bend back.
Step Three: Mixing the resin
Depending on the room temperature, warming the epoxy is necessary to thin down the consistency of the resin. Resin that’s too cold is like molasses. And if attempting to mix the parts, no matter how slowly you stir, you’ll trap all sorts of air bubbles. The thicker consistency also makes it hard to fully combine the two parts. Putting the resin and hardener into hot water for 15-30 minutes is a great way to warm the resin (22-25deg). Make sure you dry the resin containers thoroughly before mixing, so that no water contaminates the resin. Always mix DP4.0 resin by weight rather than volume, as the base and hardener have different weight-volume ratios. Be EXTRA vigilant to make sure you have combined the two parts properly.!! Often changing mixing containers and re-stirring is a great way to ensure no base resin is left on the bottom of the mixing pot. Try not to create too many air bubbles whilst mixing.
Step Four: Adding pigments.
This is where the fun really begins with the endless variety of possibilities. Beware of adding too much pigment! Most quality products use very little either translucent, opaque pigment, or metallic powder. Here is a good trick to see how the resin looks with your pigment mixed. Mark a clear plastic cup at the depth of the pour. Most slabs are around 50ml thick. Then fill the clear plastic cup with the mixed resin to the height of the mark you’ve made. Then you can look through the cup from top to bottom to gauge if you need to add any more pigment. Leave the resin to sit for a few minutes after mixing the pigments, before pouring the resin.
Step Five: Pouring the resin
Try to minimize the distance when pouring resin into your mould. It’s amazing how many air bubbles this seemingly simple act creates. Also, try not to overfill your river so that it fills onto the top surface of your wood. This is one of the key causes of wood “cupping” and makes flattening the table much harder.. Putting a bead of silicon at the top edge of the river is a good way to contain the resin. Pour in 10-15 millimetre stages and blow torch each layer to remove any trapped air bubbles. Beware of excessive blow torch use as it may heat the resin too much.
Step Six: Curing time
Deep pour epoxies take much longer to react and full curing may take up to 72 hours for the DP4.0 resin. Without going overboard, when part A and part B are mixed a chemical reaction occurs, crosslinking all the molecules which in turn causes heat. One of the great things about deep pour resin is that it creates heat slowly. But...a thicker and larger area will cause more chemical reaction and therefore produces more heat. Too much heat will cause the resin to exotherm (overheat) which can ruin your entire project. If pouring in very large volumes, think about doing two pours. Pours of up to 4 inches-100ml are no problem, as long as void areas (Rivers) are narrow. Problems caused by overheating include cracks, bubbles and resin shrinkage. Temperature obviously plays a huge part in how quickly or slowly the reaction happens, and it’s recommended to pour in temperatures between 17 and 25deg. If it’s a big pour, try to keep the room cool (17-19 deg) for the first 48hrs. For these larger pours, it is also essential to have a fan removing any warm air from above the table created by the resin curing. If at 48hrs the resin is still rubbery, you will need to add more heat to get it to fully harden. Do not wait till after 72hrs to do this. Personally I like the low and slow approach where I keep the room cool for the first 24-48hrs, and then increase the temp on the third day if required.
Step Seven: After applying the resin.
It is recommended to blow-torch or heat gun the top surface once you have poured your resin to get rid of any air bubbles. Always keep the torch moving fast, and never get too close to avoid baking the resin. If pouring in warm temperatures, beware of heating up the resin too much while doing this.
Extra notes:
Metallic pigment pours require a little more work as you need to keep stirring the resin as it sets. You will see that when you first stir, it looks great. But come back 30min later and it’s gone flat. This is typical of all epoxies and the key is to get the resin just as it’s starting to stiffen and change from a liquid, to a jelly.
Translucent pours are quite hard to not get air bubbles in. The key here is to warm the wood prior to sealing it, and again before pouring your deep pour. Old electric blankets are great for this.